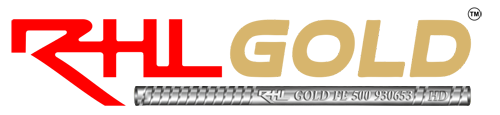
Steel is an essential element of any civil or construction activity likes Houses, Multi Storeys, Townships, Malls, Airports, Ports, Dams, and Bridges etc. Steel not only provides strength to any construction but also provides durability and long life.
Each transformation of steel industry was driven by the growing market need for steel bars with higher strength and elongation. The 21st century has witnessed a rapid increase in the cost of steel products and also brought greater focus on safety and quality norms of construction. This has spurred the demand for development for TMT bars with properties of high strength and elongation to provide cost savings in the construction by reducing consumption.
Steel researchers across the world have been working hard to develop steel products to meet these specific market needs. This research has led to development of TMT steel Bars with yield strength of 500 N/mm², 550 N/mm2 and 600 N/mm2. These bars, because of higher strength than traditional steel bars, are required in lesser quantity, thus, reducing the overall cost of structure significantly.
The BIS code for IS 1786 (High Strength Deformed Steel Bars And Wires for concrete Reinforcement Specification), IS 13920 (Ductile Detailing of Reinforced concrete structures subjected to Seismic forces - Code of Practice) and IS 456 (Plain And Reinforced Concrete – Code of Practice) incorporated necessary changes to include these latest developments in the field of steel technology.
IS 1786 under its latest revision groups the Steel Bars under the following grades:
Reinforcing steel is produced through one or combination of processes like hot rolling after micro alloying, hot rolling followed by cold working or hot rolling followed by Thermo Mechanical Treatment (TMT process).
TMT technology involves rapid cooling of hot rolled bars rolled out of a finishing rolling mill from a temperature of 950-1050°C to 550-600°C using high pressure cool water spray system. The bars after quenching are cooled under controlled atmospheric conditions to impart properties based on size and grade being rolled. The three major steps of TMT process are as under :
The hot rolled bar coming out of the finishing rolling mill stand is passed through a quenching box where it is rapidly quenched using high pressure cool water spray system. The surface of the bar gets hardened to the depth optimized for each section through formation of 'Martensitic' rim while the core remains hot and 'Austenitic'.
The bar coming out of the quenching box thus has a hot core compared to the cool outer surface thus allowing the heat to flow from the inner core to the outer surface causing tempering of the outer martensitic rim into "Tempered Martensitic" structure. The core still remains "Austenitic" at this stage.
The bar is then finished on a Automatic rake type controlled Cooling Bed where uniform atmospheric cooling of each bar takes place under controlled conditions resulting in the transformation of the hot "Austenitic" core of the bar into "Ferrite Pearlite" structure. The resultant final structure of the Bar thus produced consists of a hard and strong outer layer (Tempered Martensitic) with a soft and ductile inner core (Ferrite Pearlite) structure.
The analysis for various grades of steel is done as per relevant part of IS : 228 quality standards and maximum permissible %age of constituents are as below :-
Chemical Constituent | Unit | Fe 500 | Fe 500D | Fe 500S | Fe 550 | Fe 550D | Fe 600 |
Carbon (C) | % Max | 0.30 | 0.25 | 0.25 | 0.30 | 0.25 | 0.30 |
Carbon Equivalent (CE) | % Max | 0.42 | 0.42 | 0.42 | 0.42 | 0.42 | 0.42 |
Sulphur (S) | % Max | 0.055 | 0.040 | 0.040 | 0.055 | 0.040 | 0.040 |
Phosphorus (P) | % Max | 0.055 | 0.040 | 0.040 | 0.050 | 0.040 | 0.040 |
S + P | % Max | 0.105 | 0.075 | 0.075 | 0.100 | 0.075 | 0.075 |
• Where CE = C + (Mn/6)
• Where Mn Stands For Manganese
S.N. | CHEMICAL CONSTITUENT | CONTROLLING PROPERTY | ACTUAL EFFECT |
1 | Carbon (C) | Hardness Tensile Strength Yield Strength Weldability Brittleness |
Higher Carbon content upto 0.30% leads to higher tensile strength, Yield Strength, Elongation etc.. However, Carbon content greater than 0.30% makes the bar brittle and unweldable. |
2 | Manganese (Mn) | Tensile Strength Yield Strength Elongation Total Elongation |
Higher Manganese content increases Tensile strength, Yield Strength, Elongation and total elongation. |
3 | Sulphur | Present as impurity in steel which increases brittleness | Higher Sulphur content makes the bar brittle during cold twisting and brings hot shot problem during rolling |
4 | Phosphorus (P) | Present as an impurity which increases strength and brittleness | Higher Phosphorus content contributes to increase in strength and corrosion resistant properties but also brings brittleness to the TMT bars thereby resulting in lower life of steel. |
5 | Carbon Equivalent (CE) | Hardness, Tensile Strength and Weldability | This property is required to set the cooling para meters in TMT process and slight variation in Carbon equivalent may alter the physical property. Higher Carbon Equivalent > 0.42 leads to poor weldability of the TMT bars and corresponding reduction in life of teel. |
All the test pieces are tested for it’s mechanical properties in accordance with the IS : 1608 standard read in conjunction with IS : 2062 standards.
Properties | Unit | Fe 500 | Fe 500D | Fe 500S |
Yield Stress (YS) | N/Mm2 Min. | 500 | 500 | Min-500 Max-625 |
Tensile Stress (TS) | N/Mm2 Min. | 545 | 565 | |
Stress Ratio (TS/YS) | ≥1.08 | ≥1.10 | ≥1.25 | |
Elongation | % Min. | 12 | 16 | 18 |
Total Elongation | % Min. | - | 5 | 8 |
Bend and Re-bend Tests are performed in accordance to IS : 1599 standards.
In case of Rebend Test, the test piece is bend to an angular 135° using mandrel of appropriate diameter as mentioned below. This bend piece shall be aged in boiling water (100°C for 30 minutes) and then allowed to cool. The steel piece is thereafter bended back to an included angle of 157.5°.
Mandrel Diameter For Different Grades | |||
Nominal Size | Fe 500 | Fe 500D | Fe 500S |
D ≤ 10 | 5d | 4d | 4d |
D > 10 | 7d | 6d | 6d |
* Where d is the nominal size of the test piece in mm
Mandrel diameter of different grades of TMT bars and sizes for bend and re-bend tests are as follows :
Mandrel Diameter For Different Grades | |||
Nominal Size | Fe 500 | Fe 500D | Fe 500S |
D ≤ 20 | 4d | 3d | 3d |
D > 20 | 5d | 4d | 4d |
* Where d is the nominal size of the test piece in mm
Substantial savings not only in steel consumption, steel cost but also column area can be made by replacing Fe 415 grade steel with Fe 500 grade steel. Heavily reinforced structures like High rise buildings, Malls, Infrastructure projects like tunnels, bridges, dams, ports, air ports etc. can be ideal locations for substantial and significant steel cost/monetary savings for the steel user.
Indicative cost of Fe 415 grade steel | Rs.47,000/- |
Indicative cost of Fe 500 grade steel | Rs.51,000/- |
Higher Yield Strength in % | 20% |
Effective Steel cost in use of 415 grade | Rs.47,000/- |
Effective Steel cost in use of 500 grade | Rs.40,800/- |
Savings in steel cost | Rs. 6,200/- |
Savings in steel consumption | 13.19% |
IS 1786 has incorporated specifications for higher grades of steel like Fe 550 and Fe 600 in their revised code. Few manufacturers of the country are also manufacturing the same. These higher grades have higher Yield Strength, Tensile Strength, Elongation etc. These grades will help in not only reducing steel consumption in construction but also increasing carpet area of construction by reduction of column area.
Substantial cost savings of approximate 13% i.e. Rs.6,200/- per M.T. at current steel prices are there in use of Fe 500 grade of steel as compared to Fe 415 grade of steel.
Apart from savings in steel consumption, use of Fe 500 grade of steel can increase carpet area of construction by reducing column area. These savings can further be enhanced by use of higher grades of steel like Fe 550 and Fe 600 TMT grade.
ACTIVITY | ADVANTAGE |
Steel Billet of appropriate chemical composition | Right raw material procurement and selection |
Accurate rolling within close tolerances | Robust and Accurate manufacturing equipment |
Quenching under appropriate water pressure, water temperature and water volume depending on finishing mill speed, chemical parameters, size and grade of finished steel | Trained manpower |
Uniform atmospheric cooling on Automatic rake type cooling bed | Right technology |
Testing for Mechanical, Physical properties in laboratory | Quality Assurance |
Bundling, tagging and dispatch as per grade and size of finished TMT Steel | Complete customer service and satisfaction |